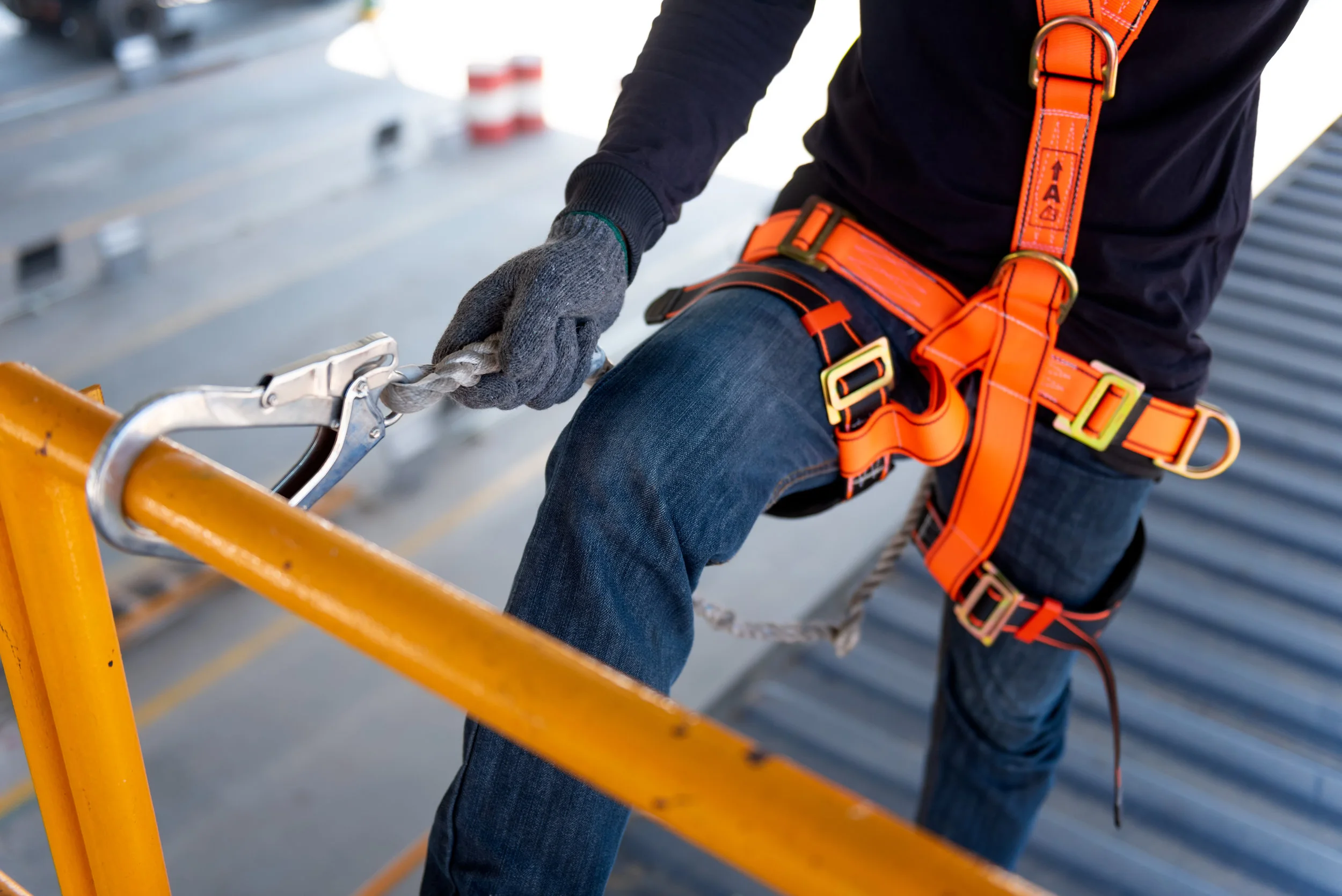
Facing the safety plateau.
Across industries and regions of the world, rates of lost work time incidents and fatalities are locked in at a steady but costly rate. Even companies with the best safety records are experiencing this plateau.
The impact to business is significant:
In 2017, EU-OSHA and the International Labor Organization revealed that worldwide work-related injuries and illness result in the loss loss of life and livelihood amounting to 3.9 % of GDP.
It is clear that safety is an enormous challenge and one that is resistant to change. More of the same safety programs will not fill the gap.
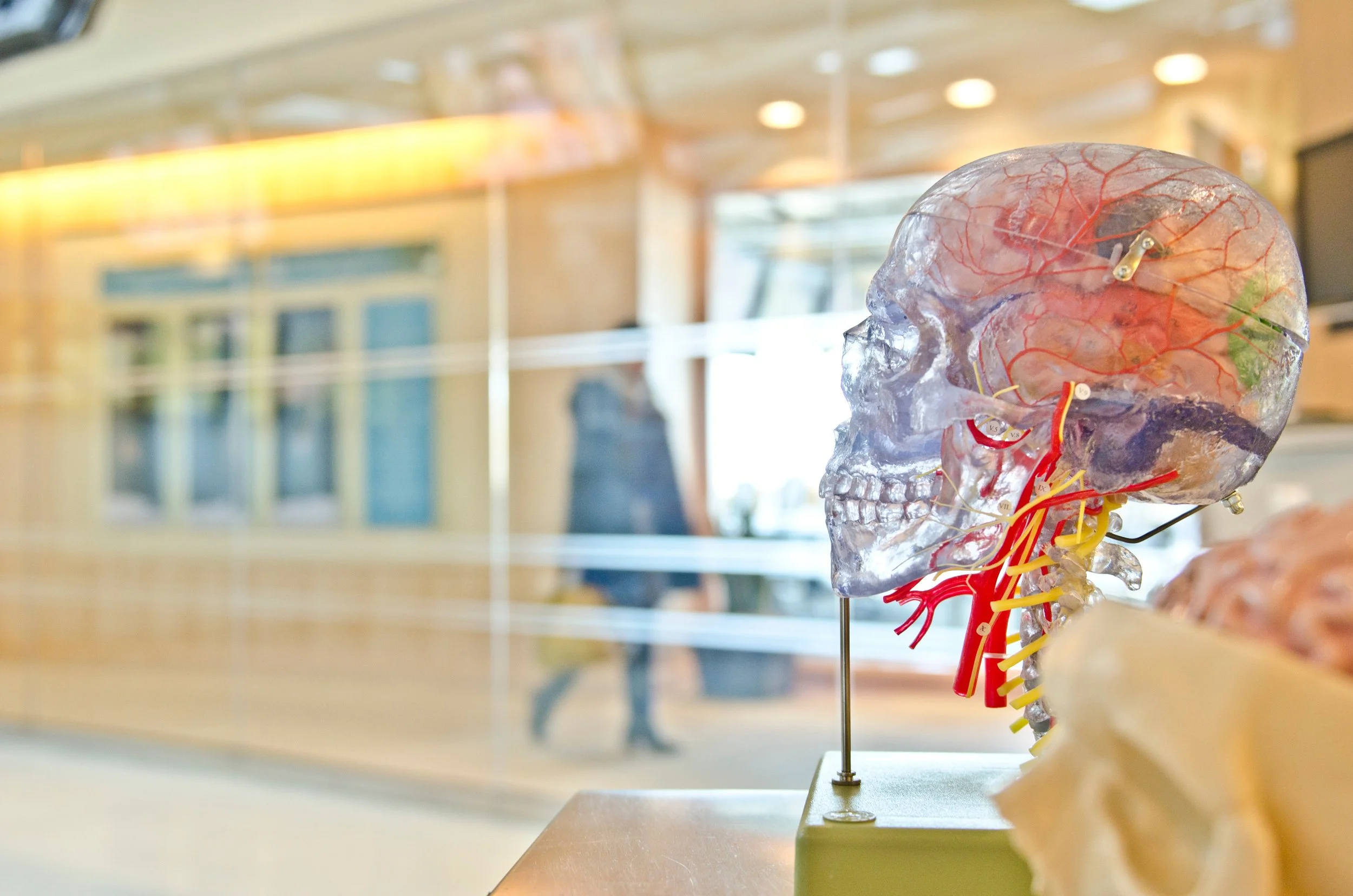
A different approach is needed.
Recent research on the human brain point to new and innovative ways of reducing work risks.
Research into the causes of accidents shows that most people who experience accidents are hurt either because they are not paying attention to risks or because they see the risks but push through them.
In one research report, nearly 90% of victims attributed their accidents to rushing, frustration, fatigue, or complacency.
It’s all about the brain:
To target these causes of accidents, we need to understand more about how the human brain works and design our safety programs with the brain in mind.
When it comes to gaining insight into our decision making, it’s useful to think of the brain as two brains.
The Thinking Brain
The thinking brain kicks in when we are alert and focused; it assesses risks and makes decisions guided by logic.
The automatic brain
The automatic brain activates when we are bored, distracted, rushed or frustrated; it reacts quickly based on habit and impulse.
Unfortunately, the vast majority of what we do is processed in the automatic brain. This can put our safety in jeopardy if we don’t find ways of coming back to full attention on a regular basis.
Our stress level determines whether we use the thinking brain or the automatic brain to make decisions. To address the threat the automatic brain poses to safety, we first teach work crew members to be aware of their moment-to-moment stress levels.
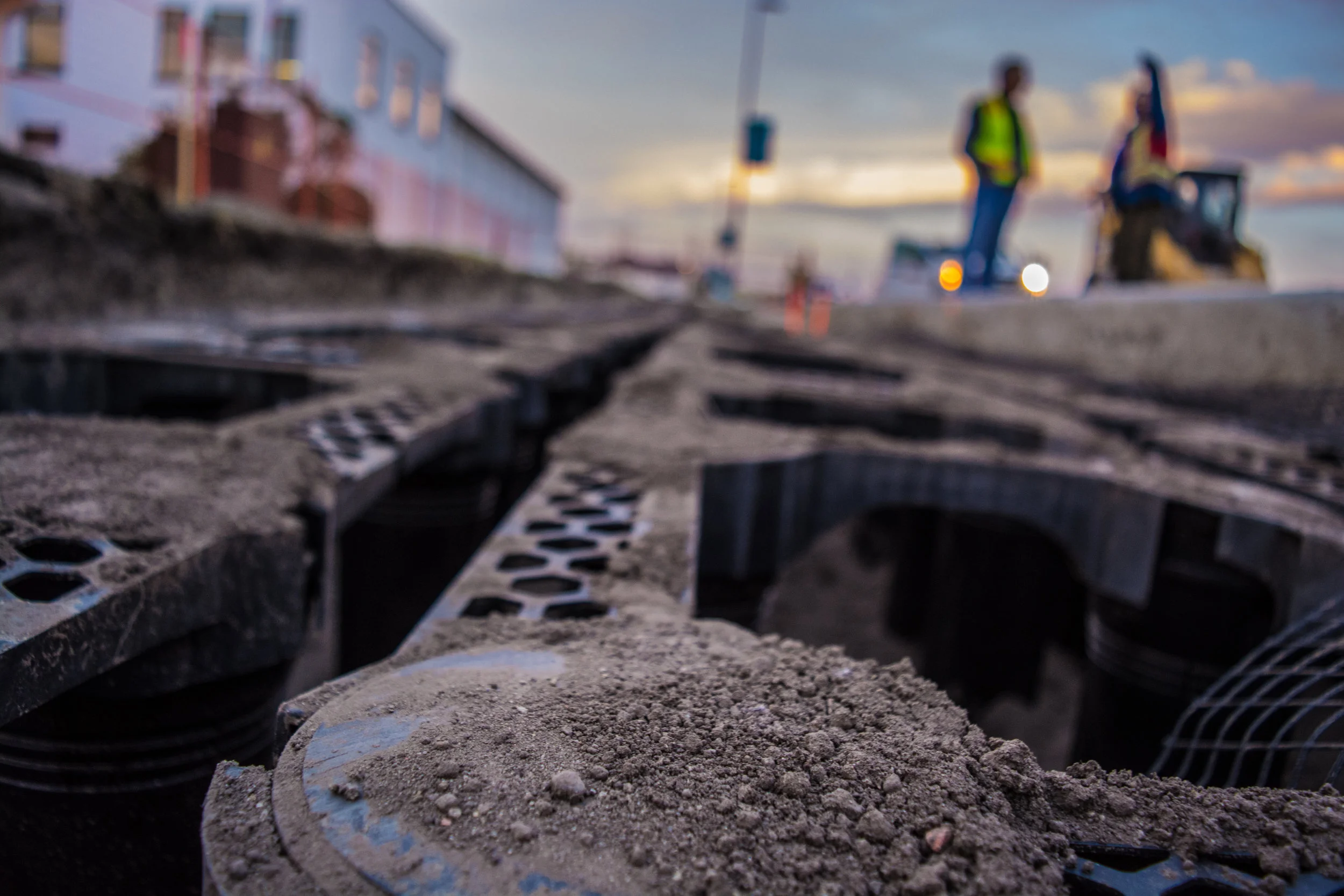
The Focus4Safety playbook.
Know your zones
This is where we begin. At any given moment, the amount of stress we’re under can be assigned to one of three zones.
The Grey Zone
In the Grey Zone, we are bored, distracted, or tired and disengaged from the present moment. The automatic brain is likely to take over, making us and those around us less safe.
The Green Zone
In the Green Zone, we are present, alert, and excited. Staying in the Green Zone as often as possible limits the amount of time the automatic brain has control over our behavior and safety.
The Red Zone
In the Red Zone, we are some mixture of anxious, frustrated, alarmed, and afraid. The automatic brain is likely to take over, making us and those around us less safe.
Anyone who spends time on a construction site has seen evidence of the two “automatic” zones—the Grey Zone and the Red Zone.
People in the Grey Zone may walk through a red barricade, fail to notice a load above them, leave a building without PPE, or walk into the path of a reversing truck.
People in the Red Zone may try to speed up work by skipping a permit or failing to tie off properly at heights. In these cases, we often ask “what were they thinking?” In fact, not much thinking is happening when the automatic brain is in control.
The Regulation Curve
Each of these zones is mapped onto a curve. The Regulation Curve is a useful picture of the moment to moment results of our brain’s responses.
The U-shape of the curve shows us that living and working under a certain amount of stress is not only normal, but helpful—it drives us towards our goals.
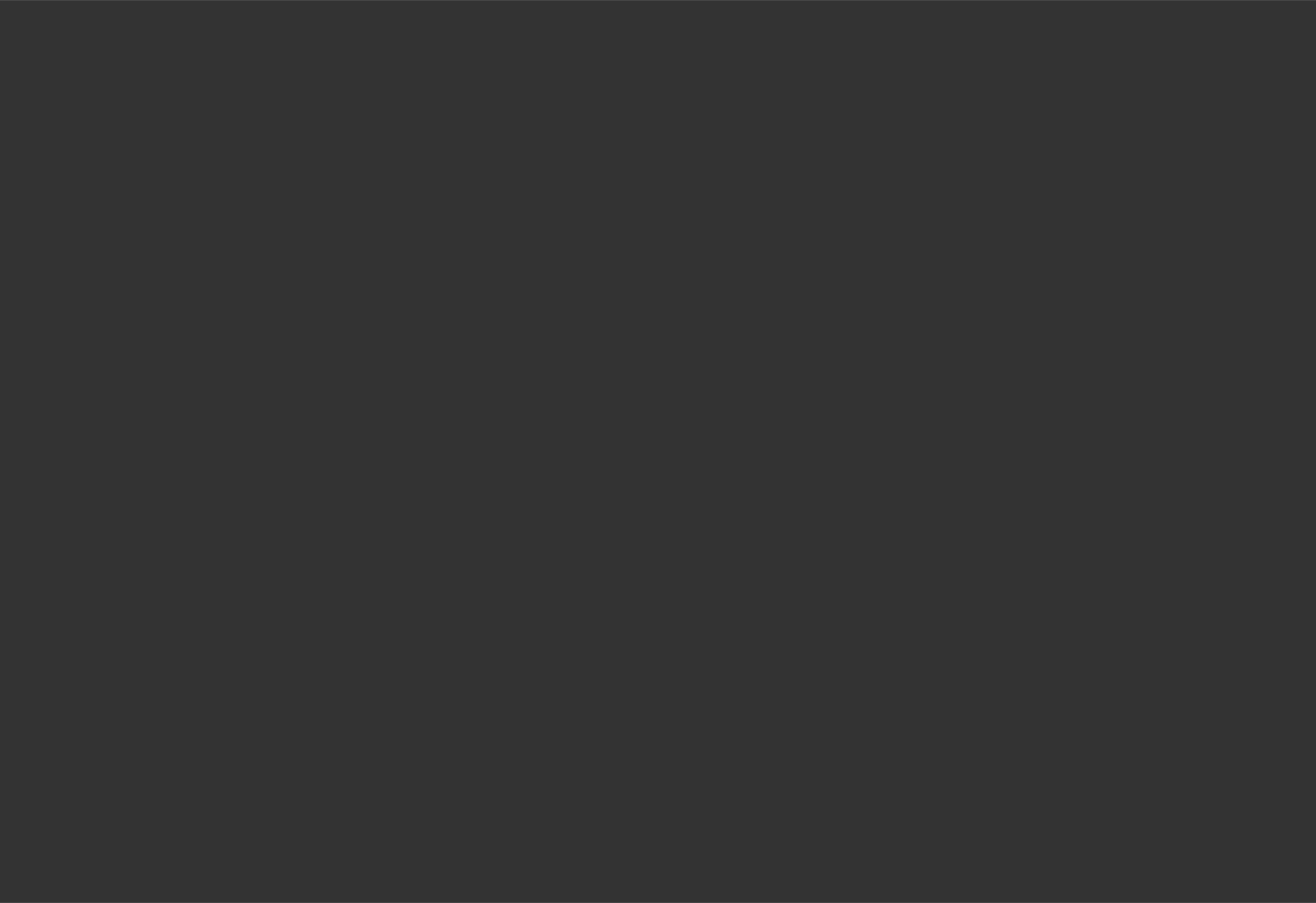
getting to the green
Our approach is to enhance existing safety management programs and processes to bring repeated attention to immediate risks and controls for specific work activities in the workplace. Our Focus4Safety playbook pinpoints four techniques that help workers overcome risk due to natural drift and stress levels.
1
Applying micro-goals in daily work activity planning to keep worker attention on task and on safety risks
3
Regulating negative emotions to stay out of the Red Zone
2
Learning to identify drift and ways of bringing workers back to full attention on a regular basis
4
Engaging safety professionals, supervisors, and workers in tracking the quality of daily risk management and giving frequent feedback on use of the above tools
The Card
The pocket-sized Focus4Safety card enhances traditional work plan controls, incorporating mindfulness with other emotional intelligence practices.
The cards ask individuals to respond to prompts throughout the day with a written response. These responses are reviewed and rated for quality. Card quality ratings are submitted to field leaders and safety professionals who give feedback to supervisors and crews. Quality ratings are linked to individuals, which allows managers to identify areas of strength and opportunity on an individual level.
Supervisors are expected to check in with crews to review the cards and to provide feedback directly on how well the controls identified on the card are being implemented. These check-ins support accountability and bring teams back to the Green Zone throughout the day.
Daily Routine
The Focus4Safety card is embedded in a daily routine that starts prior to the work day when Foremen or other leaders complete the work activity plan and enter the key tasks to be done. The crew then takes responsibility for identifying risks and controls and signing the card.
The crew is expected to review the card throughout the day (especially when changes occur). Supervisors are expected to review the card multiple times to assess progress and implementation of risk controls. These check-ins bring the crew back to full attention and provide opportunities for positive or corrective feedback as needed.
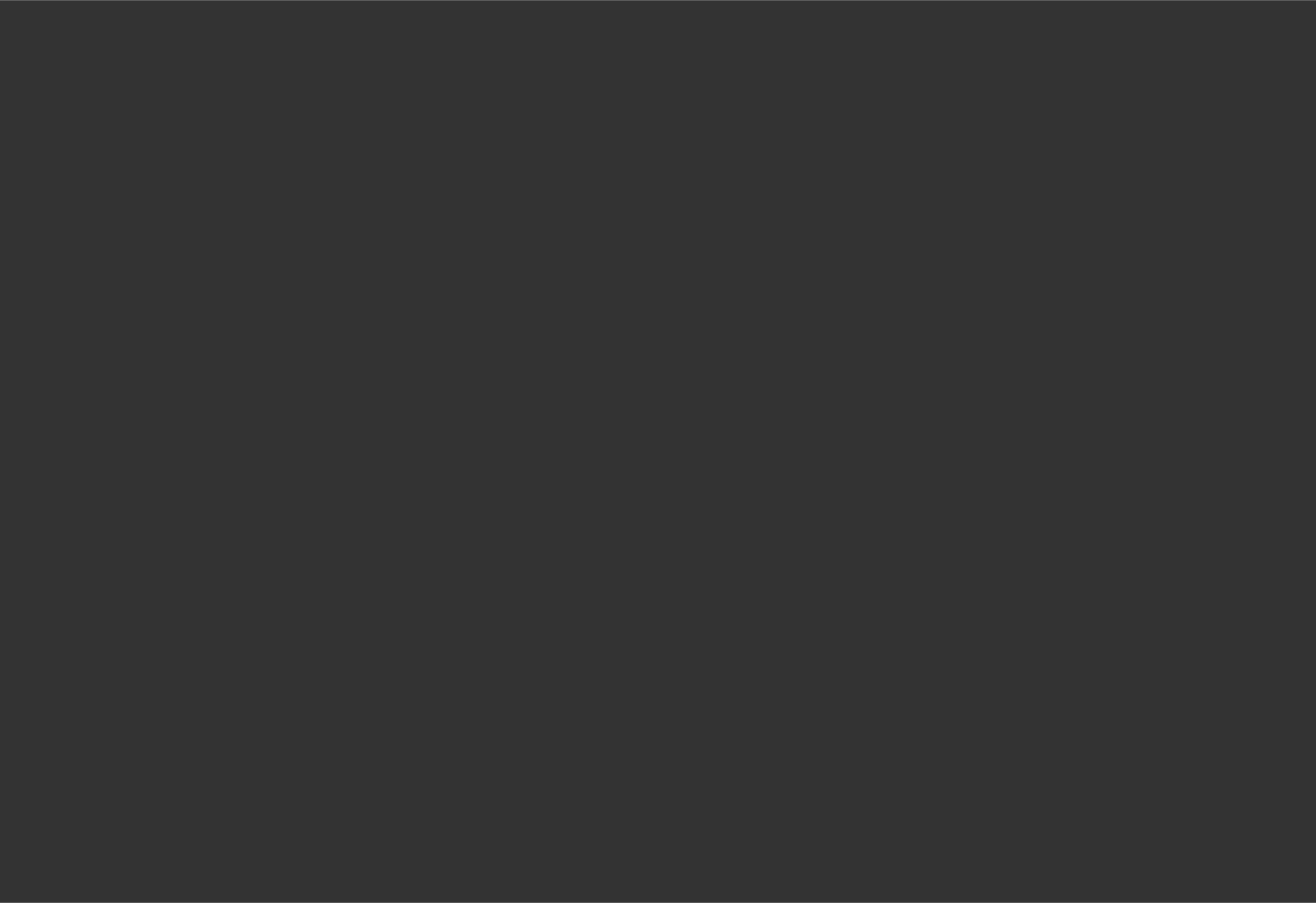
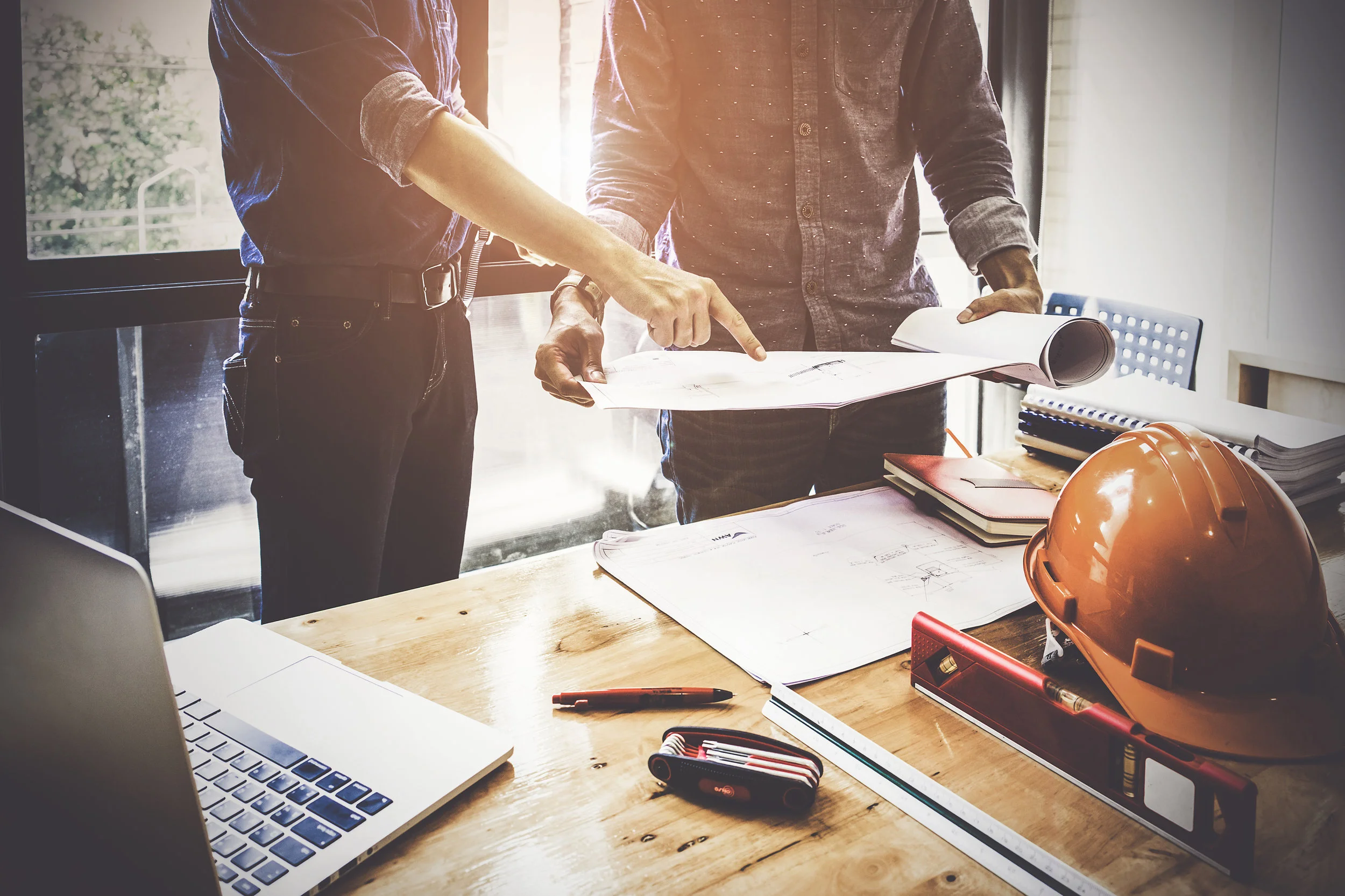
Implementing Focus4Safety.
The timeline below details a typical approach for implementing the Focus4Safety playbook, including The Card and Daily Routine.
All levels of management and supervision are involved in the process, including safety professionals who provide coaching and support in the field as the process is implemented and assessed.
Team members also have a key role in helping each other identify and manage risk and in managing the zones and attention to controls. Daily Routine and The Card are viewed as multipliers for existing safety programs, not as replacements.
Plan the implementation
Convene roadmapping session with senior managers and safety leaders
Develop a plan for communication, training, and coaching
Review the plan with supervisors and safety advisors to get their buy-in
communicate plan & launch process
Convene employee forums to explain the plan, implementation schedule, and their roles
Complete Focus4Safety workshops for all supervisors
Conduct launch forums to notify workforce of new process start-up; launch Focus4Safety Cards and new Daily Routine
Provide feedback & Manage Accountability
Collect Focus4Safety cards and rate quality by week; identify strengths and weaknesses in card quality
Provide feedback to work area managers and supervisors based on card ratings; provide average ratings by individual supervisor to area managers and safety advisors for follow-up coaching
Transfer process ownership to internal safety management for long-term sustainability
Accountability at crew level:
A critical part of Focus4Safety is strong accountability for risk analysis and controls at the crew level. This is accomplished in three ways:
Quality of Follow-through
The Focus4Safety cards are reviewed throughout the day by safety professionals and rated for quality. Each panel on the card receiving a rating of 1-5 where 5 is highest quality. These ratings are submitted for each work unit and provided to both field leaders and safety professionals, who give feedback to supervisors and crews.
Since supervisors are identified for each work activity on each card, quality ratings are linked to individuals and allow managers to identify areas of strength and opportunity by individual.
Ongoing Check-ins
Supervisors are expected to check in with crews to review the cards and to provide feedback directly on how well the controls identified on the card are being implemented. Also, managers at all levels are encouraged to ask teams to see their card as they walk through and to ask questions and provide feedback. These managers are not expected to provide formal ratings of quality (this is done by safety professionals only), but check-ins are critical to supporting accountability and in bringing teams back to the Green Zone.
Peer Support
Team members are expected to check in with each other throughout the day by reviewing the cards and updating risk reviews and controls especially if conditions change (e.g., other teams move into their work area, the weather changes, the work shifts to a different location, etc.). Also, team members are encouraged to become their “brother’s keeper” and come up with signals to get everyone to stop and look around for a few seconds several times throughout the day to take stock of the changing risks.
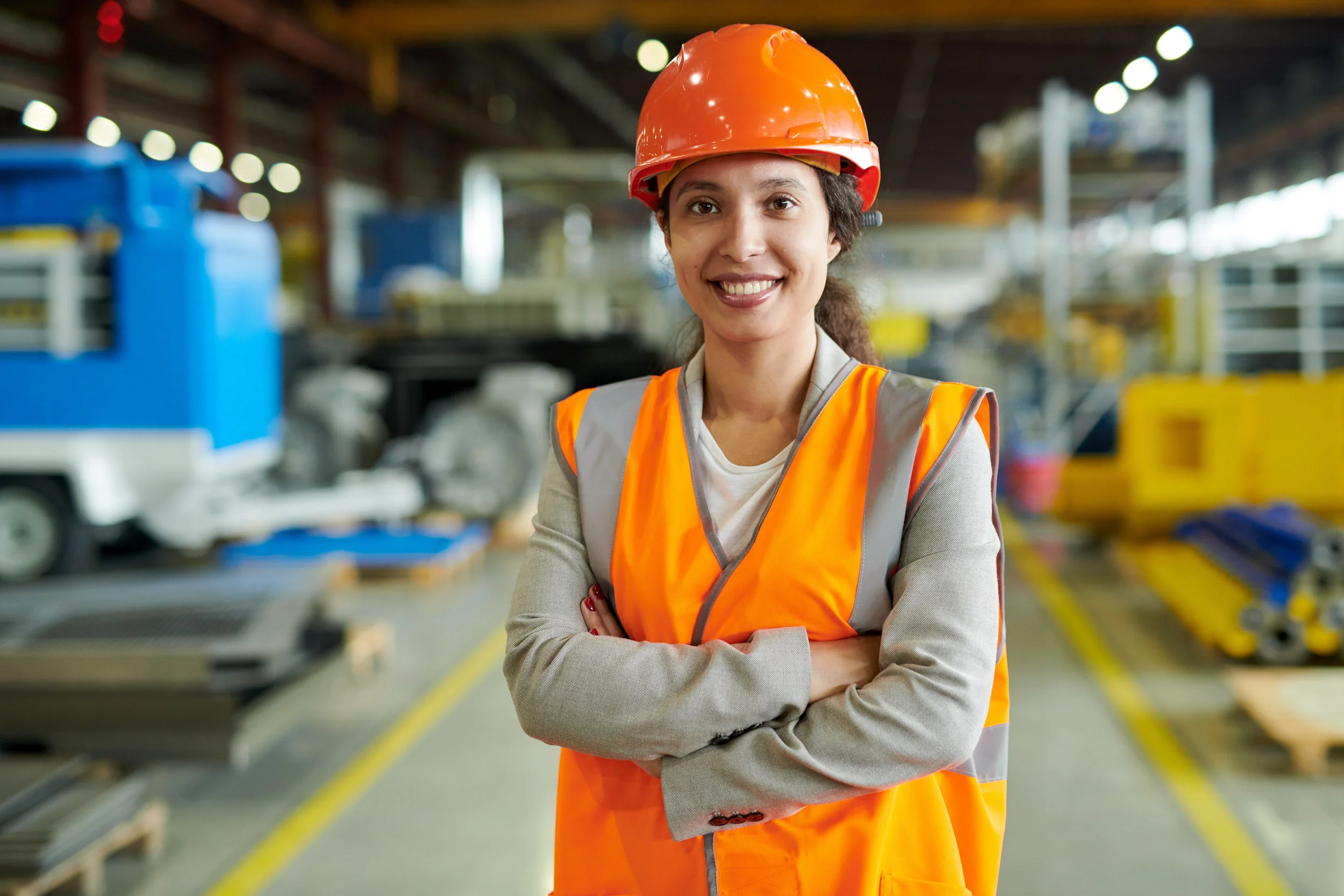
The impact of Focus4Safety.
The Focus4Safety process has been well-received by field supervision and crews who feel that the cards and daily routine help them get clear on work plans and control risks at the workplace.
In a recent application of Focus4Safety with more than 2,000 construction leaders, the workforce was supportive and the process improved safety performance.
Leaders who participated in our focus workshop and coaching reported ratings of 4.8 out of 5.0 for both the usefulness of the content and their preparation to apply the process. When asked what they planned to do differently as a result of the learning experience, many mentioned ways of changing habits to manage zones and increase attention to risks.
Here is some of what supervisors said they’d do differently after Focus4Safety training:
“I will talk more with the crew about specific tasks and check for understanding.”
“I will watch for and initiate conversations with workers when I think they are in the Grey Zone.”
“I will appreciate my crews more.”
“I will give better instructions on how to conduct work.”
“I will engage in conversations to keep people in the Green Zone.”
“I will pay attention to how I react to situations to keep people out of the Red Zone.”
Teams report that they like the cards and feel the cards are superior to traditional checklist formats because they provide a way for the group to discuss the work, review conditions, and collectively identify potential risks. Also, card quality ratings demonstrate that most supervisors and crews can implement the process immediately after the brief workshop and a single all-hands session.
We have seen evidence that higher quality on the Focus4Safety card content is correlated with lower incident rates. In one implementation involving several hundred supervisors for a 5-month period, safety incidents for individuals were significantly lower for those with higher card quality ratings.
Because the cards were linked to supervisors by name, we were able to provide recognition for higher performers and corrective coaching for lower performers. We feel strongly that tracking quality for individual supervisors and providing appropriate feedback and consequences is critical to creating a vigilant and safe work environment.